Demystifying the Process of Fabrication de pcb: From Design to Final Product
What is meant by fabrication de pcb?
- Fabrication de pcb is the process of making a printed circuit board (PCB) from a design idea. A PCB, which acts as a platform to connect and support multiple electrical components, is essential to electronic devices. An actual board with exact copper traces, channels, and connectors that permit the movement of electricity is created by fabricating a design layout. The first step in the process is to convert the design into digital information, or “Gerber files,” which control the manufacturing equipment. The substrate is made of a base material, frequently fiberglass, with a thin coating of copper. The copper is covered with a solder mask, a protective covering, leaving certain portions exposed for component connection.
- Etching, which involves carefully removing extra copper to create the correct circuit layout, is at the heart of manufacturing. Vias, or tiny conductive holes, are made to connect the PCB’s various layers. The copper is given a surface polish to prevent corrosion. A rigorous testing process is used to ensure the integrity and performance of the produced board. Since PCB manufacture directly affects the performance and dependability of electronic gadgets, which have become an essential part of our everyday lives, it calls for accuracy, skill, and attention to detail.
Making a PCB: Putting Designs into Practice
The intricate pathways that link and power the parts that power our gadgets are known as printed circuit boards, or PCBs, and they are the foundation of contemporary electronics. PCB manufacture is the critical stage in converting a design into a real, usable circuit board. A functioning and dependable board is made through a series of exacting and complex stages called “ fabrication de pcb.” Everything starts with the design stage when engineers utilize specialized software to draw a schematic of the configuration of the circuit. After that, this design is converted into files that direct the fabrication procedure.
- The production process begins by stacking a copper sheet over a fiberglass substrate material. A laminate is then created by melting the glue and joining the layers. The copper is covered with a photosensitive substance called a solder mask, which protects it while only exposing the copper’s surface where soldering occurs. The extra copper is removed from the board during the subsequent etching procedure using chemicals or milling equipment.
- The copper traces connecting the components are left behind. Vias, little holes stuffed with conductive material, link the board’s various layers and allow electricity to flow. The last procedure includes cutting the board into the proper shape and adding a surface finish that shields the copper from oxidation. PCB manufacturing links an electronic device’s functional designs to a screen. The dependability and performance of the finished product are determined by the accuracy and skill needed in each phase, highlighting the crucial significance of fabrication in electronics.
Understanding PCB Fabrication: From Design to Final Output
Printed Circuit Boards (PCBs) are the unsung heroes in contemporary electronics who make it possible for our gadgets, from cellphones to spaceships, to operate without a hitch. These technological wonders are created behind the scenes through a complex procedure called PCB manufacturing. We will demystify the PCB production process in this article by illuminating the processes involved in turning a concept into an actual, useful PCB.
- Design Phase: Innovation Blueprinting:
The journey starts with a notion for an electronic circuit that has the potential to ease daily life or transform an industry. Design engineers create a digital blueprint of the circuit’s architecture using specialist PCB design tools. The elaborately drawn copper lines that will allow the passage of electricity are also included in this layout, in addition to the locations of the components.
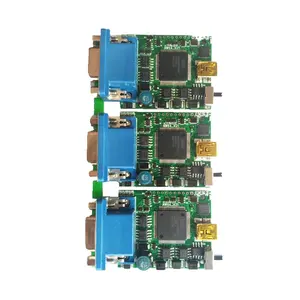
- The Bridge to Fabrication: A Gerber Files Translation
The design is converted into a series of files once it has been completed. These files provide details regarding copper placement, solder mask, silkscreen, and other topics for PCB manufacture. These files illuminate the manufacturing procedure that follows.
- Creating the Base: Copper and Substrate Layering
The basic but crucial substrate material, frequently comprised of fibreglass, is the foundation for actual manufacturing. The substrate is then heated, and an adhesive is used to adhere a thin sheet of copper to it, creating a laminate. This copper layer supports the dense web of electrical channels that will eventually grace the board.
- Vias: Connecting the Gaps
Vias are used in modern electrical circuits because they frequently need tightly packed components. Laser technology is used to drill or produce these tiny holes filled with conductive material. Vias provide communication between several PCB layers, enabling complicated and small designs.
- Surface Treatment: Protection from the Elements
PCBs are subject to various environmental elements, and oxidation is a powerful foe. The surface finish is a shield put on top of the exposed copper traces to prevent corrosion and extend the life of the board.
- Cutting and testing are the last touches:
The created PCB is now prepared for finishing touches with the complex pathways and components in place. Precision routers or milling machines are frequently used to shape the board precisely. However, it must pass stringent testing before being certified fit for use. To ensure the performance and dependability of the board, each connection is examined, each component’s functionality is confirmed, and any possible problems are fixed.
- Application of a Solder Mask: Securing the Routes
Consider the solder mask to be our PCB’s shield of defence. The copper layer is covered with this photosensitive substance, except for the spots where components will be connected. This protects the copper traces from the elements and ensures that during assembly, the solder only adheres where it should.
- Carving the Copper Canvas via Etching:
The etching procedure is at the core of fabrication de pcb. The extra copper from the board is painstakingly removed using chemical solutions or fine milling tools, leaving behind the complex web of copper traces that connect components. Precision is necessary for this phase since errors might stop the current from flowing and destroy the PCB.
The Amazing Advantages of PCB Fabrication:
Printed Circuit Boards (PCBs) are the unsung heroes in the constantly changing world of electronics, powering everything from our cell phones to heavy equipment. The elaborate patterns are brought to life through a crucial process called PCB manufacturing, which is at the center of this technical wonder. Let’s explore the outstanding advantages of fabrication de pcb to the electronics industry.
- Precision Engineering:
The manufacture of PCBs is a precision symphony. It includes etching copper lines with microscopic precision, guaranteeing interference-free transmission of electrical impulses. Electronics with excellent performance and efficiency are the result of this accuracy.
- Customization:
The level of customization possible with PCB manufacturing is unmatched. Engineers may create circuit boards with layout, component placement, and trace routing that are optimized for particular applications. This adaptability enables devices to satisfy specific requirements, whether a small wearable gadget or a large aircraft system.
- Compactness:
PCB manufacturing is largely responsible for the miniaturization of electrical equipment. The capacity to design complex paths across numerous layers allows for the creating of small, powerful devices. PCB manufacturing is essential for producing space-saving designs, from the thin profiles of modern smartphones to the sleekness of medical implants.
- Increased Functionality:
Complex circuitry is possible with PCBs because of their multilayer nature. Designers can include several functionalities into a single board by connecting layers with vias. Devices with several functionalities, like contemporary cameras, which combine image processing, connection, and power management on a single PCB, demonstrate this adaptability.
- Less Interference:
When making PCBs, signal integrity is carefully taken into account. Electromagnetic interference is reduced using ground and power planes, well-placed traces, and other techniques. Electronics less vulnerable to noise will have clearer signals and better overall performance.
- Quicker Prototyping:
PCB fabrication’s simplified procedure expedites product development and prototyping. Now that ideas can be easily turned into real boards for testing and improvement, the days of labour-intensive wire wrapping are long gone.
- Dependability:
The organized aspect of PCB production improves electronic device dependability. Consistent manufacturing procedures provide consistent outcomes, which lowers the possibility of faults and guarantees that the finished product works as intended.
Conclusion:
PCB manufacturing is a magical process that transforms a simple concept into a working electronic marvel. Modern electronics need a high level of artistry and engineering skills, as seen by the accuracy and attention to detail needed at each stage. The art and science of fabrication de pcb are also evolving along with technology, allowing us to harness the potential of invention in previously unthinkable ways. So, the next time you hold a smartphone or gaze at a spacecraft’s control panel, think back on the complex PCB fabrication process that made it all possible. NewHonest strengthens controls on filthy water, exhaust fumes, dins and solid wastes to minimize environmental influences.