Introduction of Production of pcb
Introduction to Production of pcb:
The Production of pcb is a meticulously orchestrated process that transforms raw materials into the intricate and vital components that power our modern world. From the initial design and material selection to the final assembly and testing, every step is a testament to human ingenuity and technological advancement. The next time you interact with your electronic devices, take a moment to appreciate the remarkable journey that a simple PCB has undertaken to make your life easier and more connected.
The Intricate Process Behind the Production of PCB
We frequently take for granted the technological devices that run our lives in today’s tech-savvy society. Production of pcb, used in everything from cellophanes to computers to coffee makers that prepare your daily brew, is the hero of these gadgets. Modern electronics are supported by PCBs, which offer a space-saving and effective way to link various electrical parts. But have you ever thought about the complex procedure for making these vital parts? We’ll dig into the intriguing world of PCB production in this essay, a trip that turns raw ingredients into the brains of your devices.
- Create the Blueprint
A PCB’s journey starts long before it is produced. A computerized layout of the board’s design serves as the first step. To create this digital map, designers use specialized software. This blueprint outlines the traces or paths taken by electrical connections, in addition to the structure and positioning of the components. In PCB design, every millimetre counts since effective functionality and performance depend on careful planning.
- Choosing the Correct Materials
PCBs are available in various sizes and forms, each designed for a particular use. The selection of materials is crucial and is influenced by several elements, including the intended purpose, financial limitations, and performance requirements. The most often utilized substance is FR-4, an epoxy resin with fiberglass reinforcement that balances electrical and thermal qualities. Copper is used as a thin layer on the substrate because of its great conductivity.
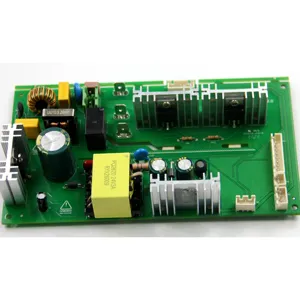
- Putting the Design into Practice
It’s time to put the design into action now that it’s finished. A copper-clad board is produced by laminating the copper layer onto the substrate. A photosensitive etching resist defines the electrical connection paths on the copper surface. This resist will safeguard those regions except for the locations where copper traces should be removed.
- Taking a Picture
A photo mask, a physical template replicating the traces and component locations on the PCB, is made using the digital design file. The photosensitive resist-coated board is covered by this mask, which is then subjected to UV light. The UV light hardens the resist in regions that the mask does not cover. After exposure, the resist that wasn’t exposed is removed, exposing the board’s pattern of traces and pads.
- Embossing the Waste Copper
It’s time to etch away the extra copper now that the pattern has been etched on the copper-clad board. An etchant solution is used to etch the board, frequently containing ferric chloride or ammonium persulfate. This solution selectively dissolves the unprotected copper, leaving the desirable copper traces in place. This etching procedure must be precise to prevent over- or under-etching and guarantee that the traces preserve the proper size.
- Exploring Connections
Computer-controlled drilling machines are typically used to drill holes into the board at specific positions carefully. In addition to fitting component leads and mounting gear, these holes connect various levels in multilayer PCBs. The drill bits must be properly packed to protect the board and guarantee accurate hole diameter.
- Bridge Construction Using Through-Hole Plating
Through-hole plating is used in multilayer PCBs where traces must pass through many layers. In through-hole plating, the walls of the drilled holes are coated with a conductive substance, frequently copper. Establishing electrical connections between the PCB’s inner layers makes more complicated circuitry possible.
- Protecting Oneself from the Elements
A solder mask shields the copper trades on the PCB from oxidation and accidental soldering. The only exposed traces and component pads are covered by the solder mask, which is typically green. It is an insulating layer, defending against environmental variables and preventing electrical short circuits.
- Finishing the Project
The PCB’s surface is printed with logos, component reference designators, and other crucial details during the subsequent stage of silkscreen printing. This knowledge benefits in maintenance and troubleshooting and assisting assembly personnel to arrange components on the board properly.
- The Production Line
The adventure continues after the creation of the PCB. The electronic jigsaw puzzle has more pieces than these boards. The assembly of components onto the PCB is the next stage. Components are accurately positioned on the board using automated pick-and-place equipment, and their placement is then secured using various soldering methods, such as reflow or wave soldering. In this stage, the expertise and accuracy of assembly professionals are essential.
- Distribution and Packaging
The PCBs must be packaged and ready for delivery during the last part of the journey. These PCBs, which enable the everyday use of technology, might, depending on the size of manufacture, be found in a variety of electronic devices, from cell phones to medical equipment.
Innovation at the Core of PCB Production: Unlocking the Benefits
Production of pcb is a pillar of technical development in electronics, where invention is the lifeblood of progression. The cornerstone of the digital world is made up of these modest boards, which are frequently concealed under further layers of components. Beyond their outwardly modest look, PCB manufacture offers many benefits that reverberate throughout sectors and significantly influence our everyday lives. The considerable benefits that PCB fabrication delivers to the forefront of technology and innovation will be shown in this investigation.
Precision engineering is at the core of PCB fabrication. Each trace, pad, and component footprint are perfectly positioned by the design parameters on every PCB, thanks to the rigorous attention to detail that goes into its creation. Every PCB is a mirror copy of the one before because this perfection is continually upheld across lengthy production cycles. This regularity is crucial, especially in industries like aircraft, telecommunications, and medical equipment, where exact electrical connections are essential.
- Consistency and accuracy
Precision engineering is at the core of PCB fabrication. Each trace, pad, and component footprint are perfectly positioned by the design parameters on every PCB, thanks to the rigorous attention to detail that goes into its creation. Every PCB is a mirror copy of the one before because this perfection is continually upheld across lengthy production cycles. This regularity is crucial, especially in industries like aircraft, telecommunications, and medical equipment, where exact electrical connections are essential.
- Space-Saving and Compact Designs
Compact and efficient electrical devices may be made thanks to PCBs. The miniaturization of technology is made possible by its capacity to pack components and traces onto a single board. Consider how cell phones are getting smaller and how computers have slimmer forms. These sleek and portable electronics are made possible in large part by PCBs.
- Durability and dependability
The production of PCBs is characterized by dependability. The strength and lifespan of PCBs are guaranteed by using premium components like fiberglass-reinforced epoxy (FR-4) and carefully chosen conductive metals like copper. These boards are designed to survive the rigors of regular usage, including mechanical stress and severe temperatures, without losing their functionality.
- Improvement of Signal Integrity
Due to PCB production’s signal integrity optimization, electronic devices can correctly send and receive data. Critical signals, such as those in high-speed data transfer or medical equipment, are guaranteed to keep their integrity by reducing signal interference and noise through controlled impedance traces and appropriate grounding procedures.
- Complexity of Multilayers
The capacity to design intricate, multi-layered boards is one advantage of PCB fabrication. These multilayer PCBs have many layers linked by vias and through-hole plating and placed on top of one another. Due to the incorporation of advanced circuitry made feasible by this design flexibility, complex electronics such as high-performance microprocessors and memory modules may be produced.
- Efficiency of Cost
The foundation of cost-effectiveness in electronics is mass manufacturing. PCB manufacturing enables economies of scale since it is possible to produce dozens or even millions of similar boards with just modest increases in production costs. Consumers benefit from this cost-effectiveness by having access to and the ability to afford technology.
- Quick iteration and prototyping
By allowing for quick prototype and iteration, PCB fabrication speeds up innovation. Designers and engineers can rapidly translate their conceptual ideas into real prototypes, test them, and refine their designs to enhance performance and usefulness. In disciplines like product development and research, this iterative approach is important.
Conclusion:
The hero of the electronics industry who propels innovation, connection, and technical advancement is the Production of pcb. Thanks to its benefits, which range from accuracy and dependability to cost-effectiveness and environmental sustainability, it affects practically every part of our lives. PCBs are the foundation of our future digital society; they are more than just circuit boards. NewHonest shines as a beacon of dependability, efficiency, and innovation in the PCB manufacturing sector. With their cutting-edge infrastructure, steadfast commitment to quality, and customer-centric approach, they have cemented their position as an industry leader. Partnering with a company like NewHonest ensures that your PCB requirements are met and exceeded, taking your creations to new heights as technology develops quickly. For a universe of options for your electrical activities, go to our website at NewHonest Strength immediately.