The Building Block of a Successful Product Development Journey is PCBA prototype
What is a PCBA prototype?
PCBA prototype is an acronym for “Printed Circuit Board Assembly prototype.” It describes a prototype or early version of a printed circuit board (PCB) that has been built, filled with electronic parts, and tested to see how well an electronic device or product performs. Before going on to mass manufacturing, engineers and designers must test their concepts using PCBA prototypes as a key phase in product development.
What is the significance of the PCBA prototype?
Making new ideas into working prototypes is a critical first step for product development and commercial success in today’s fast-paced technology environment. The Printed Circuit Board Assembly (PCBA) is the brains of any hardware prototype for electrical devices. Modern electronics are built on this complex web of parts, and designing a PCBA prototype is both an art and a science.
- Conceptualization:
The journey starts with an idea, a ground-breaking notion for a new technological device. The PCBA is the building block of all modern IoT devices, medical equipment, and gadgets. Precise schematics and diagrams map the components, connections, and power needs.
- Selection of Components:
Choosing the appropriate components is crucial. Cost, availability, and performance considerations must be made carefully. Electronic engineers choose components with great care to ensure they suit the project.
- PCB Design:
The crucial third phase is the PCB layout. Designers physically assemble components and trace them on the board using specialized software. Precision is necessary since errors might cause delays or functional problems.
- Prototype Fabrication:
The prototype board may be made after the PCB design is complete. Surface-mount technology (SMT) and through-hole assembly are two examples of advanced manufacturing processes. After assembly, the board is thoroughly tested to find any flaws or performance problems.
- Testing and Improvement:
Testing is a never-ending process. Engineers examine the prototype’s behavior as it operates after being powered up. Any problems are resolved by changing the design and using new parts. The PCB will only operate perfectly once this iterative procedure is completed.
- Scaling and iteration:
Once the prototype is flawless, it may be copied for large-scale manufacturing. Testing and quality control must be ongoing, even in large manufacturing, to maintain constant performance.
The PCB Assembly Prototype Process: From Concept to Reality
Electronic gadgets are a crucial component of our everyday lives in today’s tech-driven environment. Printed circuit board assemblies (PCBAs) constitute the foundation of these electronics, from cell phones to smart appliances. However, have you ever considered how these complex electronic circuits function? This blog will walk you through every step of the intriguing PCB assembly prototype creation process, from conception to completion.
- Conceptualization and Design:
Starting with a concept, a PCB assembly prototype is created. Whether it’s a ground-breaking new device or a vital part of a bigger system, conceptualizing the design is the first step. Engineers and designers collaborate to define the PCB’s primary functions and purpose throughout this stage. Thorough schematics, circuit diagrams, and component inventories are produced to direct the design process.
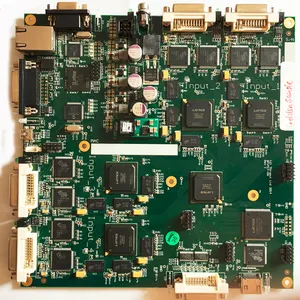
- Component Choice:
It’s time to choose the components that will go on the PCB after developing the design. This is an important phase since component selection significantly impacts the final product’s performance, dependability, and cost. When designing, engineers take into account things like component availability, power needs, compatibility, and cost-effectiveness. They might also need to consider any industry-specific rules or requirements that relate to the gadget they are developing.
- PCB Layout:
The design step may start after it is apparent what the PCB will be used for and what components it will contain. The actual layout of the PCB, which includes component placement, trace routing, and the specification of ground and power planes, is created. PCB design is a meticulous, challenging procedure that calls for accuracy and knowledge. To ensure the PCB performs as intended, engineers must consider elements like signal integrity, electromagnetic interference (EMI) mitigation, and temperature management.
- Fabrication of prototypes:
Bring the prototype to life when the PCB design is complete. This entails creating the actual PCB from scratch. The PCB is filled with components using cutting-edge manufacturing processes, including surface-mount technology (SMT) and through-hole assembly. The most popular technique, surface-mount technology (SMT), involves employing pick-and-place devices to attach small surface-mount components to the board. Contrarily, through-hole assembly entails slipping component leads through PCB holes and soldering them into position.
- Assembly and Soldering
A crucial stage in the PCB building process is soldering. The solder must be melted to establish electrical connections between the components and the PCB. Through-hole components are normally soldered manually or with wave soldering equipment, whereas surface-mount components are often soldered using reflow ovens. The soldering procedure must be exact to establish strong electrical connections and avoid flaws like solder bridges or cold joints.
- Testing and Inspection:
The PCBA prototype is thoroughly inspected and tested once the components have been soldered into place. This involves visual examinations for soldering flaws, such as solder balls or misplaced components. One can also utilize X-ray and automated optical inspection (AOI) to find concealed flaws. The PCB is put through functional testing after a visual examination, during which time it is powered up, and its behaviour is scrutinized. Any problems or inconsistencies are noted and dealt with.
- Refinement and Debugging
A PCB assembly prototype seldom operates flawlessly on the first try. Issues that need to be fixed are frequently discovered during the testing process. To identify and resolve these problems, technicians and engineers collaborate. This might entail changing out defective parts, tweaking the design, or improving the PCB layout. The prototype will be improved until it satisfies all performance and reliability standards.
- Scaling and iteration:
The prototype may be copied for mass production after it functions perfectly and satisfies all design requirements. The prototype must be duplicated in order to scale up manufacturing, and this procedure must preserve consistency and quality. Quality control procedures are put in place to guarantee that every PCB assembly leaving the manufacturing line meets the same high requirements as the prototype.
- Compliance and documentation:
Thorough documentation is crucial for the PCB assembly prototype process as a whole. This includes documenting component specs, design modifications, test outcomes, and compliance-related data. Documentation is essential for future reference, troubleshooting, and ensuring the product conforms with industry standards and laws.
- Constant Development:
The creation of a PCB assembly prototype is a continuous process. The design and manufacturing methods are always improved, even after mass production starts. Field feedback, customer experiences, and technological advancements can all influence improvements and updates to PCB design and assembly methods.
What are the applications of the PCBA prototype?
Prototypes of printed circuit board assemblies (PCBAs) link creative concepts and useful electrical gadgets. These prototypes are essential to many businesses because they allow engineers and designers to test their ideas, find flaws, and prepare for successful mass production. Let’s look at some of the main uses for PCBA prototypes.
Electronics Industry:
The electronics industry itself is the most apparent use for PCBA prototypes. Electrical products, including cutting-edge smartphones, powerful laptops, and cutting-edge IoT devices, begin as prototypes. PCBA prototype assist manufacturers in honing their designs, maximizing component selections, and guaranteeing that the finished product satisfies performance and quality requirements.
Automotive Technology:
These prototypes are essential for creating cutting-edge vehicle systems in the automotive sector. These prototypes allow the testing of important parts, including infotainment systems, sensors, and engine control units (ECUs). Additionally, they enable the implementation of cutting-edge technologies by automakers, such as electric propulsion systems and autonomous driving capabilities.
Medical Devices:
These prototypes are crucial to the development of medical devices, from diagnostic tools to life-saving gadgets like pacemakers. Medical device makers employ prototyping to test the precision of sensors, the dependability of circuitry, and the usability of the devices. It’s essential in a sector where accuracy and dependability are key.
IoT and Embedded Systems:
The Internet of Things (IoT) and embedded systems rely on compact, effective, dependable electrical components. The sensors, communication modules, and microcontrollers that power IoT devices are developed using these prototypes. Iterative prototyping optimises overall functionality, connection, and power usage.
Consumer electronics:
Consumer electronics, such as smart TVs, gaming consoles, and wearable technology, require thorough testing and validation using these prototypes. In order to make sure that the finished product lives up to consumer expectations, manufacturers test prototypes for things like power efficiency, thermal management, and user interface design.
Conclusion:
A successful PCBA prototype shows how ideas may become reality via careful planning, exact execution, and steadfast commitment. Learning the art of this prototype is crucial in the always-changing field of electronics, whether you’re a startup hoping to disrupt the industry or an established business trying to stay ahead. With the knowledge that quality and dependability would be the pillars of our technical innovations, NewHonest company uses these PCBAs.