Custom PCB Factory: Making Your Custom PCBs
Wenshu Custom PCB Factory, a PCB supplier and manufacturer located in Dongguan City, Guangdong Province, has been operating for 26 years. The company consistently exceeds expectations thanks to its experience in the industry.
Our commitment as professional PCB manufacturing service providers revolves around delivering top-notch quality, cost-efficiency, and punctual deliveries. Our niche specialization lies in producing small to medium-sized quantities (ranging from 1 to 200 pieces) of printed circuit boards and their associated components.
Moreover, our company boasts a team of skilled engineers primed to address your project needs. We have state-of-the-art facilities that provide an excellent environment for all your PCB assembly and testing needs.
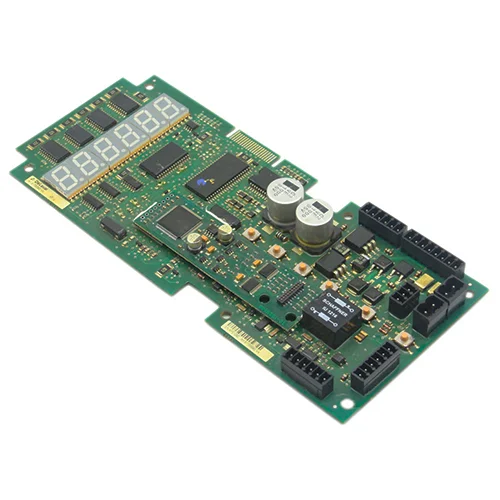
Prototyping & Design Services: The Foundation of Excellence
The inception of our PCB design services occurs when clients or engineers furnish PCB design files outlining the board’s layout, components, and interconnections. Manufacturers carefully examine these design files before manufacturing begins. CUSTOM PCB FACTORY
Prototyping – An Essential Step in the Process
Prototyping is the process of creating models or mock-ups to validate functional and design requirements before moving on to build a system. It serves as a vital tool in the development process, helping identify and rectify potential issues. Prototypes are fashioned through various methods such as hand wiring, machine wiring, or printed circuit boards (PCBs). Software simulations may also be employed to evaluate performance before actual prototype construction.
Materials Procurement Expertise
We offer a spectrum of materials procurement options tailored to meet your specific requisites. You can opt for us to source materials on your behalf or purchase them directly from our trusted suppliers:
Copper-clad Laminate Sheets: We provide copper-clad laminate (CCL) sheets sourced from various vendors to cater to your unique requirements. Our standard sheets measure 1/16″ in thickness and feature a nickel over copper finish, although we also offer thicker grades with gold or tin over copper finishes.
Solder Paste: Our choice for prototype work is Chemtronics solder paste, a product purpose-built for PCB assembly, devoid of lead.
Solder Mask: For prototypes, we utilize Chemtronics solder mask products, known for their ease of application without the need for baking in an oven before component attachment.
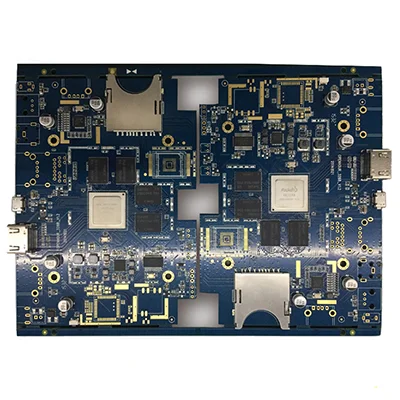
Printed Circuit Board Manufacturing – A Multistep Process
PCB fabrication involves several pivotal steps, including:
– Printing the Copper Pattern:
We apply copper to laminate sheets, followed by the application of a protective solder mask layer. The imprint of the circuit design is then transferred onto the board, shaping copper traces in accordance with the circuit design.
– Etching:
Unwanted copper is removed from the board using an acid etching process. In some cases, a second layer of photo-resist may be applied, allowing both layers to be etched simultaneously, facilitating intricate circuit patterns.
– Drilling:
The holes in the PCB are used to house components and establish electrical connections. Drilling can be manual or automated, with automated machines offering faster, more precise results at a higher cost.
– Plating:
Copper is plated onto hole walls to establish conductive pathways between layers, particularly for multilayer PCBs. This process entails depositing a thin, electrically conductive metal layer onto another material’s surface, creating a robust conductive path.
– Solder Mask and Silkscreen:
The application of a solder mask insulates copper traces and prevents short circuits. The silkscreen layer includes component labels and reference information.
– Final Inspection:
The ultimate step involves a comprehensive examination of boards for quality, dimensional accuracy, and potential defects. Final inspection is a crucial step, as it allows you to note any issues and document them in a technical report for review. CUSTOM PCB FACTORY
Testing and Quality Control
Our PCBs undergo rigorous testing, encompassing electrical and functional evaluations to ensure they align with design specifications. Electrical tests confirm that circuit traces do not leak current or voltage between connections, while functional tests verify that the board functions as expected. CUSTOM PCB FACTORY
The Significance of Inspection in Quality Control
Inspections are integral in identifying and rectifying defects, playing a pivotal role in quality control. Inspections may be carried out by both humans and machines, detecting issues that may elude the human eye.
Customer Feedback and Iteration
Client feedback serves as an invaluable tool for enhancing our manufacturing processes and PCB design. It often takes many iterations to fine-tune a design before it’s ready for production.
CONCLUSION
We recognize that several factors influence PCB fabrication applications, ranging from design complexity to cost-effectiveness. Our extensive experience in the field positions us to assist you in finding the optimal solution to meet your unique demands, reflecting our unwavering commitment to mutual development and improvement. Our commitment is to deliver excellence. CUSTOM PCB FACTORY