-
Capability
-
DIP Plug-in Processing Capabilities
ltem | Capability |
---|---|
Order Quantity | ≥1PC |
Quality Grade | IPC-A-610 |
Lead Time | 24 hours expedited service can be offered. 3- 4 days normally for PCBA prototype orders. We will give you an accurate lead time when we quote for you. |
Size | 50*50mm~510*460mm |
Board Type | Rigid PCB, Flexible PCB, metal core PCB |
Min Package | 01005 (0.4mm*0.2mm) |
Max Package | No limit |
Mounting Accuracy | ±0.035mm(±0.025mm) Cpk≥1.0 (3σ) |
Surface Finish | Lead/Lead-free HASL, Immersion gold, OPS, etc. |
Assembly Types | Surface mount (SMT), Through-hole (DIP), Mixed Technology (SMT & Thru-hole) |
Component Sourcing | Turnkey (All components sourced by Wenshu), Partial turnkey, Kitted/Consigned |
BGA Package | BGA Dia. 0.14mm, BGA 0.2mm pitch |
SMT Parts Presentation | Cut Tape, Partial reel, Reel, Tube, Tray, Laser-cut Stainless Steel |
Cable Assembly | We supply custom cables, cable assemblies, wiring looms/harnesses and power leads for various industries including automotive, security, mining, medical and entertainment. |
Stencil | Stencil with or without frame (offered free by Wenshu) |
Quality Inspection | Visual inspection; AOI checking; BGA placement – X-RAY checking |
SMT Capacity | 3 Million~4 Million Soldering Pad/day |
DIP Capacity | 100 Thousand Pins/day |
The Dual In-Line Package (DIP) plug is a widely used method for integrating electronic components onto printed circuit boards (PCBs). It offers a straightforward and efficient approach to electronic assembly, particularly for discrete components and integrated circuits (ICs). The DIP plug method involves the utilization of DIP packages, which consist of individual electronic components encapsulated within rectangular housings with two parallel rows of pins. These pins are designed to fit into corresponding sockets on the PCB, creating a secure and reliable electrical connection.
Advantages of DIP Plug-In Technology:
- Versatility and Modular Assembly: The DIP plug-in method provides a high degree of versatility and modularity in electronic assembly. Electronic components can be easily inserted or removed from DIP sockets, enabling rapid prototyping, testing, and system modifications. This flexibility simplifies design iterations and facilitates maintenance and repairs.
- Time and Cost Efficiency: One of the major advantages of the DIP plug-in technique is its time and cost efficiency. Unlike traditional soldering methods, DIP plug-in does not require complex soldering equipment or processes. This reduces setup time and labor costs. Moreover, the ability to quickly replace faulty components contributes to faster repair turnaround times, minimizing downtime.
- Accessibility for Testing and Debugging: DIP plug-in technology offers easy accessibility to components for testing and debugging purposes. During the development phase, engineers can swiftly insert or remove components to assess their functionality and identify any issues. This accessibility streamlines the troubleshooting process and accelerates the resolution of problems.
- Component Compatibility and Interchangeability: DIP packages are designed with standardized pin configurations and socket layouts, making them compatible with a wide range of electronic components. This interchangeability simplifies component sourcing, inventory management, and system upgrades. Engineers can easily swap components to suit evolving requirements.
- Reliable Electrical Connections: DIP sockets establish reliable electrical connections between components and PCBs. The pins and sockets are designed to create secure contacts, ensuring consistent signal transmission and minimizing the risk of loose connections or intermittent faults. This reliability is crucial for maintaining signal integrity.
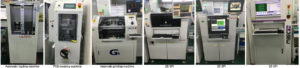
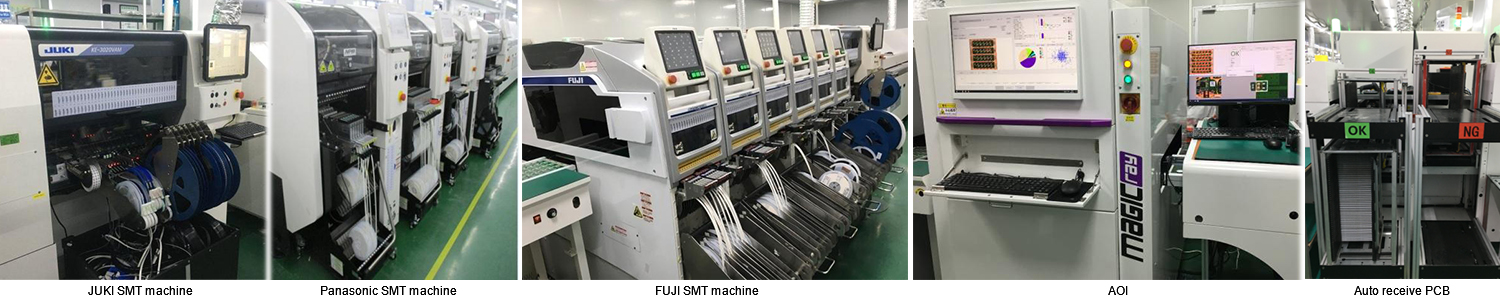
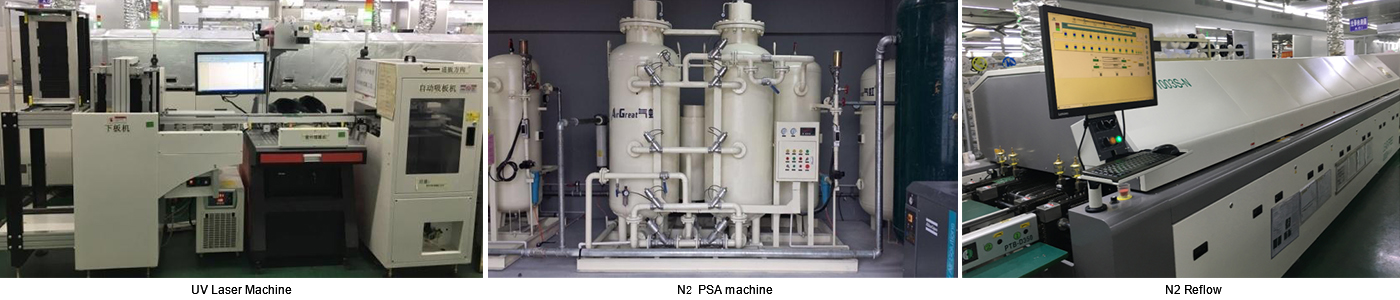
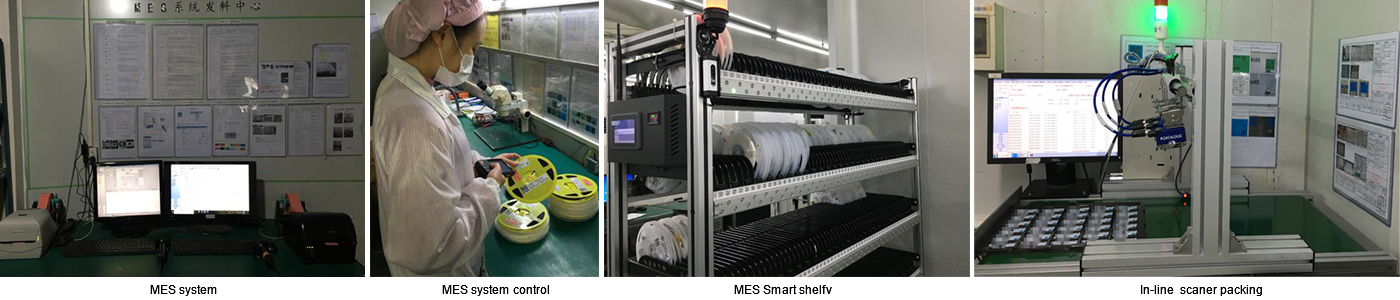
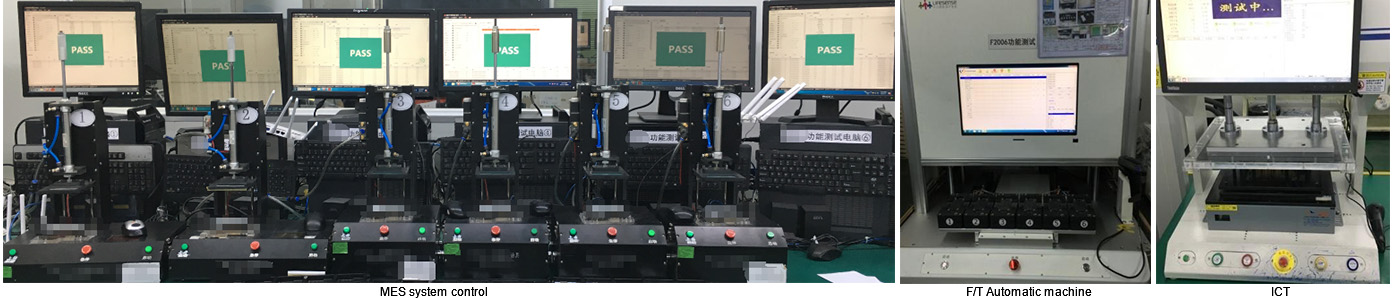