The Incredible Benefits of Fabrication PCB for Your Electronics Projects
The introductions of fabrication pcb:
One fundamental component—printed circuit boards or PCBs—remains constant in a world where technology is evolving quickly and setting the pace of development. At the core of every electrical device we use, these modest yet complex products orchestrate the symphony of impulses that make our devices function. In this investigation, we explore the art and science of fabrication pcb, exposing the covert processes that turn raw materials into the brains of our digital life. Consider your smartphone as the svelte, smooth gateway to the digital world. An intricate web of conductive channels linking chips, capacitors, and resistors may be found hidden behind the shiny shell of the device. This symmetrical beauty results from the painstaking interaction between design and manufacture, where creativity and accuracy are united.
A blueprint is engraved in virtual space at the beginning of the voyage. Engineers carefully design the arrangement while using advanced algorithms to direct the route of the electrons like a master architect. The substrate material choice becomes increasingly important as the design comes into focus. The selection affects the board’s signal integrity, thermal performance, and physical characteristics. The canvas becomes reality after the design is set. The finely woven copper layers that cover the substrate spread out to carry the electric currents that fuel our modern lifestyles online. This flat surface is transformed into a three-dimensional work of art by etching, drilling, and plating, ready to hold the parts that determine its function.
The Key to Effective and Reliable Electronics is PCB Fabrication:
The Printed Circuit Board (PCB) is the brain of every electronic device in the dynamic field of electronics. The foundation of contemporary electronics is made up of these complex networks of conductive channels, which allow for smooth communication and interaction between diverse parts. The effectiveness, usability, and dependability of electronic devices are critically influenced by the PCB production process.
- Getting to Know PCB Fabrication:
The process of building a physical board that supports and links electronic components via a web of copper lines is known as PCB manufacturing. Using Computer-Aided Design (CAD) software, engineers were able to precisely arrange the architecture of the components and the routing of the connections for this linked maze of conductive channels.
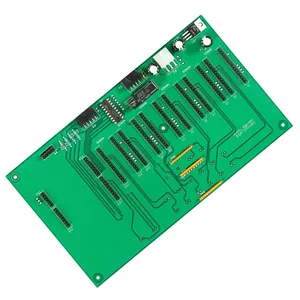
- Precision through Efficiency:
Size, power use, and signal integrity are all examples of characteristics that affect how efficient an electronic device is. By enabling engineers to create small layouts, assuring less signal loss, and improving the flow of power, PCB manufacture directly affects these features. Advanced production methods, such as surface mount technology (SMT) and multilayer PCBs, make it feasible to construct complex structures with a small physical footprint and a high degree of efficiency.
- Reliability Is Important:
Electronics depend on reliability since broken equipment might have serious repercussions. By maintaining constant quality, fabrication pcb considerably increases the reliability of electronics. Copper traces must be precisely etched, solder masks must be applied in a controlled manner, and component holes must be carefully drilled. By taking these precautions, the likelihood of short circuits, bad connections, and other problems that can affect the device’s operation is reduced.
- Materials Can Change the World:
A key component of PCB manufacture is selecting the appropriate materials. Electrical and thermal characteristics of the board are influenced by the substrate material, sometimes referred to as the PCB foundation. A common substrate material that balances performance and cost-effectiveness is FR-4. Materials like ceramic or flexible substrates, on the other hand, could be selected for particular applications where heat dissipation or signal integrity is essential.
- Advanced Performance Enhancing Techniques:
Technology development has opened the door for cutting-edge manufacturing methods that push the limits of performance. The narrower trace widths, for instance, are used in High-Density Interconnect (HDI) PCBs, which enable more intricate and compact designs. This makes it possible to miniaturize gadgets even more without sacrificing functionality.
- Observing environmental regulations:
PCB manufacture has adopted ecologically friendly procedures in the age of sustainability. For example, lead-free soldering techniques are increasingly accepted as best practices to lessen the environmental effect of electrical trash. To produce more environmentally sensitive PCBs, manufacturers are also experimenting with recyclable and biodegradable substrate materials.
- Coordination and revision:
To build reliable and effective electronics, engineers, fabricators, and PCB designers collaborate. The layout and connectivity of the PCB are improved through iterative design procedures that entail prototyping and testing. Prototyping services provided by contemporary fabrication pcb facilities enable engineers to test their concepts before mass production, saving both time and resources.
A Closer Look at the World of Printed Circuit Boards: Understanding the PCB Fabrication Process
Printed Circuit Boards (PCBs) are the unsung heroes of modern electronics, providing the electricity that keeps our gadgets running smoothly. These complex circuit boards act as the vital link between numerous parts and guarantee the smooth flow of electrical impulses. Let’s explore the intriguing world of PCB manufacture and the complex procedure that creates these modern wonders.
- Create the blueprint:
The process of fabricating PCBs starts with careful planning and design. Engineers arrange the parts and traces on the board using specialist Computer-Aided Design (CAD) software. Choosing the best positioning for connections, components, and copper traces that will transmit electrical signals are all part of this process. The usefulness and efficiency of the finished product are built on the precision of this design phase.
- Choosing the Proper Materials:
After the design is complete, choosing the right materials is an essential next step. The basis of the whole board is made by the substrate material, often known as the PCB base or PCB laminate. Cost, signal integrity, and heat conductivity are influenced by the material choice. FR-4, an epoxy laminate reinforced with fiberglass, and more specialist choices like Rogers materials for high-frequency applications are examples of materials that are often utilized.
- Copper Layer Formation and Etching:
A complex web of copper traces that promotes the movement of electrical current is a PCB’s defining feature. The substrate is coated with copper throughout the manufacturing process, and any excess copper is subsequently carefully removed via etching. The exact traces needed to build connections between components are left behind during the etching process, which follows the pattern specified in the design.
- Stacking Layers for Complexity
A single-layer PCB might not be sufficient for more complicated electrical gadgets. Multilayer PCBs come into play in these circumstances. These boards are made up of many substrate layers, with an insulating substance separating each layer. Vias, which are tiny holes filled with conductive material, are used to link the layers. Modern high-performance electronics require layer stacking because it enables more useful and compact designs.
- Plating and drilling:
As it makes holes for mounting components and establishes connections between various layers of a multilayer board, drilling is a crucial stage in the production of PCBs. To promote continuous communication, the holes are frequently coated with conductive material after being drilled. The reliability and performance of the finished board are improved via through-hole plating and cutting-edge methods.
- Testing and quality control:
The constructed PCBs go through extensive quality control and testing before they are considered fit for use. To find any flaws, such as missing parts or faulty connections, standard techniques include automated optical inspection (AOI) and electrical testing. Only trustworthy and useful PCBs enter electrical gadgets thanks to this strict quality control.
The Bottom Line: The Heart of Electronics
Modern electronics are built on the complicated and exact process of PCB manufacture. The utility, effectiveness, and dependability of electronic devices are largely a result of meticulous design, material selection, and attention to detail at every stage of manufacturing. PCBs are at the center of it all, linking the digital world in ways that we frequently take for granted, whether it be in the smallest wearable technology or the most complicated communication networks.
The Amazing Advantages of PCB Manufacturing for Your Electronics:
Electronics may profit greatly from fabrication PCB (Printed Circuit Board), which makes it a crucial step in contemporary technology. Almost all electronic devices are supported by PCBs, which provide them a strong basis on which to operate and perform. The following are some major benefits of fabrication pcb:
- PCBs enable the compact integration of complex circuit designs into a single board. This device’s compactness increases overall efficiency while also saving space.
- Using PCBs decreases the possibility of human mistake during assembly and does away with the necessity for loose connections, which provides great dependability.
- When fabricating a printed circuit board (PCB), care is taken to ensure that the signal traces are consistent in length, impedance, and capacitance. This reduces signal loss and protects the accuracy of the electronic signals.
- Easy Diagnostics and Repair: Specific components on PCBs are labeled and arranged, making it simple to identify and fix any potential flaws.
- PCB fabrication makes it possible to produce electrical devices in large quantities with reliable quality while cutting down on production time and expenses.
- PCBs may be customized to meet the needs of different devices, ranging from straightforward designs to extremely complex configurations.
- By properly grounding and shielding PCBs, EMI may be decreased, which enhances device performance and lessens interference.
Conclusion:
The advantages of fabrication PCB for electronics are clear, to sum up. PCBs are essential to the development of the contemporary technological landscape, improving signal integrity, dependability, and enabling customization in addition to better component integration. PCB manufacturing is still essential for creating effective, dependable, and high-performance devices as electronics continue to advance. To reduce impacts on the environment, we tighten controls on dirty water, exhaust fumes, noise, and any solid wastes. NewHonest also set targets and concrete guidelines for environmental controls and continuously assess the outcomes of environmental activities in order to make improvements.