The Intricate Process of PCBA Manufacturing: From Design to Assembly
Electronics Revolutionizing: The Fascinating World of PCBA Manufacturing
Manufacturing printed circuit board assemblies (PCBAs) is a crucial cornerstone in the fast-paced world of electronics, where innovation is the driving force. The functioning of everything from smartphones to complex medical equipment is guaranteed by PCBA production, the beating heart of electronic gadgets. Let’s delve into the fascinating realm of pcba manufacturing and examine its crucial function in our technologically advanced life. Printed circuit board (PCB) fabrication is a multi-step process that starts with creating the boards. These boards serve as the framework for mounting electrical components.
- PCBs are made in various sizes and forms to suit the particular requirements of the equipment they will power. Component installation comes next after the PCBs are completed. Specifically, microchips, resistors, capacitors, and other electronic components must be affixed to the PCB for this to work. This step’s precision and accuracy ensure the device’s dependability and performance. Soldering comes into play after component installation. By employing molten solder to join components to the PCB, soldering creates a reliable electrical connection.
- Modern PCBA production improves the quality and effectiveness of the assembly process by utilizing sophisticated soldering techniques, including reflow soldering and wave soldering. One of the most important steps in PCBA production is quality control. To find and fix any flaws or inconsistencies, thorough testing and inspection processes are used. By doing this, the finished product meets the highest performance and reliability criteria. In PCBA production, scalability is just as important as accuracy and technology. PCBA manufacturers may adjust to the needs of the market, whether they are mass-producing millions of devices or only a few prototypes.
The Delicate Manufacturing Process of PCB Assembly:
Manufacturing of Printed Circuit Board Assembly (PCBA) is a challenging and crucial procedure in the electronics industry. To build the framework for the various gadgets we use on a daily basis, printed circuit boards (PCBs) must be painstakingly assembled with electrical components. We’re going to embark on a wonderful adventure through this process.
- First step: PCB fabrication:
The manufacture of the PCB itself marks the beginning of the PCB assembly manufacturing process. In order to link and join numerous electronic components, PCBs serve as the structural foundation of electronic devices. The components’ placement and the finished product’s functioning are both determined by the PCB design, which is an essential first step. The production of the substrate, which is frequently constructed of fiberglass or another composite material, is the first stage in the multi-phase process. After bonding a layer of copper foil to the substrate, the copper traces that will be used to transmit electricity between components are defined by a protective mask. Advanced etching methods are used to remove extra copper and make the circuit’s complicated channels.
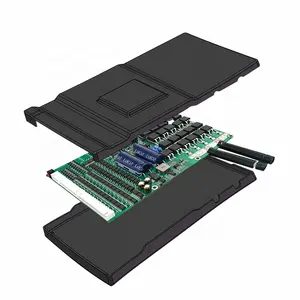
- Step 2: Purchasing and Inspection of Components:
The electrical components are purchased in the following stage after the PCBs have been manufactured. To fill the PCB, it is necessary to source the microchips, resistors, capacitors, and other components. Confirming that the components adhere to the requirements and quality standards is crucial. Inspection is a crucial part of the component purchase process. Each component must be closely scrutinized to ensure its authenticity and quality. Substandard or counterfeit parts might result in future production flaws and device malfunctions. To ensure the integrity of their components, manufacturers utilize a combination of manual inspection and automated technology.
- Step 3: Positioning Components
It’s time to begin the challenging component placement procedure with the PCBs and components in hand. Since even the smallest misalignment might cause electrical connections to break or the gadget to malfunction, this stage calls for accuracy and precision. Automated pick-and-place equipment is used in modern pcba manufacturing to accommodate various component sizes and shapes. Using specialized nozzles, these devices take up components and accurately position them on the PCB. The machines are guided by sophisticated vision systems, ensuring that parts are positioned with micron-level precision.
- Step 4: Soldering:
The soldering process turns a PCB containing components into an operational electrical circuit. Utilizing molten solder to join components to the PCB creates reliable electrical connections. Reflow and wave soldering are the two most popular soldering methods used today. Reflow soldering is heating the whole PCB in a controlled setting to melt the solder paste that has been put into it and create connections. During wave soldering, the bottom of the PCB is submerged in a molten solder bath, which forms connections by capillary action.
- Step 5: Quality Control:
In the fabrication of PCB assemblies, quality control is crucial. Stringent testing and inspection processes are used to find and fix any flaws or anomalies. Every device that leaves the assembly line must adhere to the highest performance, dependability, and safety standards. Cameras and image processing are used in Automated Optical Inspection (AOI) systems to find problems with solder connections and component placement problems. An in-depth analysis of concealed connections and components is possible with X-ray inspection. By putting the gadget through realistic settings, functional testing can confirm how well it performs.
- Step 6: Distribution and Packaging
The last phase is packaging and delivery, when the PCB assembly is finished and passes quality control. The completed assemblies are expertly wrapped to safeguard them during handling and delivery. These assemblies may be found in a variety of items, including industrial machinery, consumer electronics, and medical equipment.
What Benefits NewHonest PCBA Manufacturing: Increasing Efficiency and Simplifying Processes
Manufacturing of Printed Circuit Board Assembly (PCBA) is essential for simplifying procedures and increasing productivity in the dynamic field of electronics. The complex procedure of attaching electronic parts to printed circuit boards (PCBs) has several advantages that go beyond those of an assembly line. Let’s examine how PCBA production helps the electronics sector be more productive and innovative.
- The increased design freedom that manufacturing provides is one of its main benefits. PCBs may be modified to meet the unique requirements of a device, enabling smaller layouts, lower energy usage, and better performance. Engineers can experiment with different arrangements that can accommodate a wide variety of functionalities and form factors.
- Quality control is crucial in the production of electronics, and PCBA is no exception. Each PCB assembly is tested and inspected using cutting-edge techniques, including automated optical inspection and X-ray inspection. Early defect detection helps manufacturers save money on rework and warranty expenses, further enhancing productivity.
- Manufacturing PCBAs is very scalable. The procedure may be modified to match your needs, whether you want a small batch of prototypes or a big production run. This scalability enables businesses to react swiftly to changes in demand, avoiding excess or undersupply and maximizing resource use.
- In the electronics sector, where quick product development and quicker time-to-market are crucial, time is important. This manufacturing greatly accelerates production. Component installation and soldering are quickly and precisely handled by automated equipment, cutting down on human labour and mistake rates. This speeds up the construction of intricate electrical gadgets, providing manufacturers an advantage.
- Often, efficiency results in cost reductions. Our manufacturing helps lower production costs by utilizing economies of scale and the capacity to automate several manufacturing processes. Manufacturers can provide high-quality products at competitive rates by simplifying production and maximizing resource use.
- The dependability of a product depends on consistency. All devices have uniform quality thanks to PCBA manufacture. Automated equipment places components precisely and consistently, minimizing deviations that might cause performance inconsistencies or field failures. The same high standards will be met by all products so that customers may have confidence.
- Iterative design and quick prototyping are made possible by pcba manufacturing. Engineers can test out novel ideas and features due to shorter manufacturing cycles, speeding up innovation. This adaptability is especially crucial because of the short product lifecycles and intense rivalry in sectors like consumer electronics and telecoms.
- The possibility of human mistakes is considerably decreased by automation in pcb manufacturing. Machines conduct intricate component positioning and soldering activities with amazing accuracy. This improves the goods’ overall quality and lessens the need for rework, which may be expensive and time-consuming.
- Environmentally friendly manufacturing techniques are also efficient. A greener manufacturing process includes reduced energy use and material waste. The carbon footprint connected to the manufacture and distribution of electronic gadgets is also reduced through effective logistics and transportation tactics.
Conclusion:
The pcba manufacturing is a key component of contemporary electronics manufacturing, providing many advantages beyond the assembly line. Processes are streamlined, productivity is increased, innovation is accelerated, and product quality is improved, eventually boosting the electronics industry’s development and competitiveness. Our production will remain a crucial engine of efficiency and advancement in the electronics industry as technology develops. NewHonest defines and lays out clear objectives and benchmarks for environmental controls, and we continually assess the outcomes of environmental actions to make further advancements.